长期以来,激光技术以焊接、切割和打标的广泛使用为人们所知,这两年随着激光清洗的逐渐普及,激光表面处理的概念才越来越多地成为人们关注的焦点,出现在人们的脑海中。激光以非接触方式加工,高柔性、高速无噪声、热影响区小无损基材,无耗材且环保低碳。激光表面处理除了激光清洗之外,其实还有非常多的应用类别,例如激光抛光、激光熔覆、激光淬火等等。这些方法被用在改变材料表面的特定物理化学性能上,比如使表面加工成具有疏水性的功能,或者用激光脉冲产生直径约为10微米,深度仅为几微米小凹陷,以此来增加粗糙度、增强表面附着力等等。除了激光清洗,下面几种激光表面处理方式你都知道吗?
激光淬火是加工高应力复杂部件的解决方案之一,可以令凸轮轴和折弯工具等磨损较高的零部件承受更高的应力,延长寿命。
它的原理是通过将含碳工件的表皮被加热到略低于熔化温度(900 -1400°C,40%的辐照功率被吸收),使金属晶格中的碳原子重新排列(奥氏体化),而后激光束沿进给方向稳定加热表面,随着激光束的移动周围的材料快速冷却,金属晶格无法恢复其原始形式,从而产生马氏体,使硬度显着增加。激光硬化达成的碳钢外层硬化深度通常为0.1-1.5mm,在某些材料上可以做到2.5mm或更大。相较于传统的淬火方式它的优点在于:1. 目标热输入仅限于局部区域,因此在加工过程中几乎没有组件翘曲。返工成本减少,甚至可完全消除;2. 在复杂的几何型面和精密的部件也能硬化,可以实现传统淬火方法无法淬火的局部受限的功能表面精确硬化;3. 无失真。传统的硬化过程中由于更高的能量输入和淬火而产生变形,但在激光硬化过程中,由于激光技术和温度控制,可以精确控制热量输入。组件几乎保持其原始状态;4. 可以“即时”快速更改部件的硬度几何形状。这意味着无需转换光学器件/整个系统。激光毛化是金属材料表面改性的工艺手段之一。在结构化过程中,激光在层或基材中创建规则排列的几何形状,以便有针对性地改变技术特性并开发新功能。作用过程大致是使用激光辐射(通常是短脉冲激光)以可重复的方式在表面上生成规则排列的几何形状。激光束以受控方式熔化材料,并通过适当的工艺管理固化成确定的结构。
例如疏水性表面结构可以让水从表面流掉。用超短脉冲激光器在表面创造亚微米结构就可以实现这个特性,并可以通过改变激光参数对所要创造的结构进行精确控制。相反的效果,例如亲水性表面,同样可以实现;
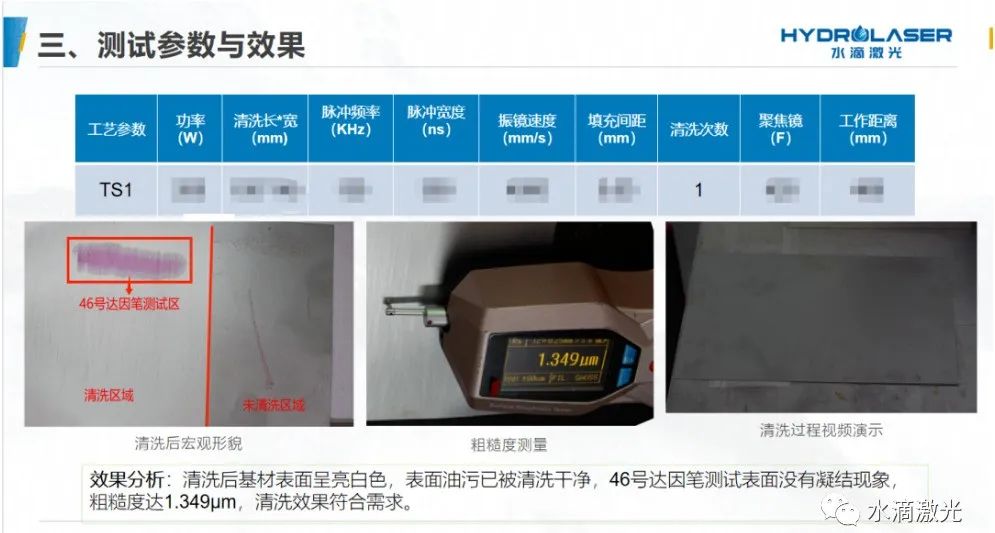
水滴激光通过相关工艺提高表面粗糙度
汽车面板要涂漆,必须让薄板表面均匀分布“微坑”以增强漆料的附着力,用每秒数千至上万次的脉冲激光束聚焦后入射到轧辊表面,在聚焦点处轧辊表面形成微小溶池,同时对微小溶池侧吹,让溶池中的溶融物按指定要求尽量堆积到溶池边缘形成圆弧形凸台,这些小凸台和微坑既可提升材料表面的粗糙度增加漆料的附着力,又可以提高材料的表面硬度,延长使用寿命。某些特性是由激光结构产生的,如一些金属材料的摩擦特性或导电导热性。此外,激光结构化也增加了工件的粘合强度和使用寿命。
相较传统方式,表面激光结构化更加环保,不需要额外的喷砂剂或化学物质;可重复且精确,激光实现了精确到微米的受控结构,并且非常容易复制;低维护,与快速磨损的机械工具相比,激光是非接触式的,因此绝对无磨损;无需后处理,激光加工的部件上不会留下熔体或其他加工残留物。
激光回火常用在激光炫彩表面处理上,又称做激光彩色打标。工艺原理是激光加热材料时,将金属局部加热到略低于其熔点,在适当的工艺参数下,此时栅极的结构会发生变化;在工件表面会形成氧化层,这层薄膜在光的照射下,入射光干涉使各种回火色在这时出现,表面生成的这一层幻彩的打标层,随着不用的观察角度而变化,标记的图案也会变幻出各种不同的颜色。
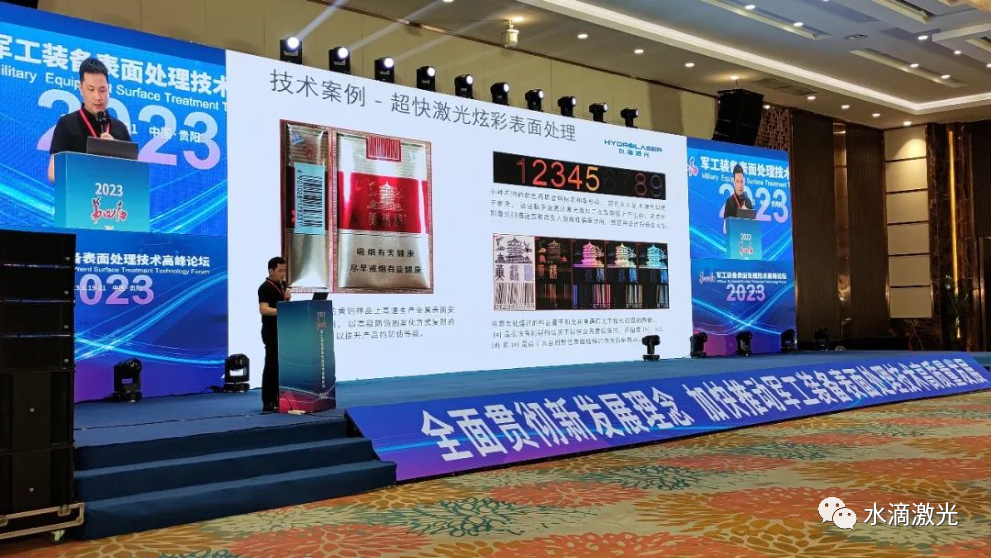
水滴激光发表关于超快激光炫彩表面处理的报告
这些颜色在高达约 200 °C 时保持温度稳定。温度更高时,栅极会恢复其初始状态—打标消失。表面质量将完整保留。在防伪的应用上具有高度的安全性和可追溯性。近年来已成熟运用于医疗技术领域,除了通过超短脉冲激光器进行全新的黑色打标外,还非常适合进行产品标识,从而根据 UDI 指令实现唯一可追溯性。
是一种适合金属和金属陶瓷混合材料的增材制造工艺。借此可以打造或修改 3D 几何形状。使用该生产方法,激光也可以进行修复或镀膜。因此在航空航天领域,增材制造被用于修复涡轮叶片。在工具和模具制造领域,可以修复破裂或磨损的边缘和造形功能表面,或者甚至是在局部加装装甲。为了防止磨损和腐蚀,在能源技术或石油化学领域,为轴承位置、滚子或液压部件镀膜。而且在汽车制造领域也使用增材制造。在此对大量部件进行改良。在常规的激光金属熔覆中,激光束先局部加热工件,然后形成熔池。然后从激光加工头的喷嘴将精细金属粉直接喷入熔池。在高速激光金属熔覆过程中,粉末颗粒在基底表面上方就已经几乎加热到了熔化温度。因此,熔化粉末颗粒只需要较少的时间。效果:明显提升流程速度。由于热效应更小,通过高速激光金属熔覆也可以为对热非常敏感的材料,如铝合金和铸铁合金,进行涂层。通过 HS-LMD 工艺可以在旋转对称表面上形成很高的表面速率,最高达 1500 cm²/min。同时实现高达每分钟数百米的进给速度。通过激光粉末激光金属熔覆快速、轻松地修复昂贵的部件或模具。大大小小的损伤都可以迅速修复,且几乎无痕。也可以更改设计。从而节省时间、能源和材料。尤其是针对昂贵的金属,如镍或钛,相当值得。典型的应用示例有涡轮叶片、各种活塞、阀门、轴或模具。数千个微型激光器(VCSEL)被安装在了单块芯片上。每个发射器上均装有 56 块这样的芯片,而 一个模块则由若干个发射器构成。矩形辐射区可包含数百万个微型激光器并且可输出数千瓦的红外激光功率。VCSEL 通过大面积的定向矩形光束横截面可生成辐射强度为100 W/cm² 的近红外光束。原则上,这种技术适用于所有对表面和温度控制精准性要求极其严苛的工业流程。激光热处理模块尤为适合精度要求严苛且灵活的大面积加热应用场景。相较于传统的加热方法,这种新型加热工艺拥有更高的灵活性、精度和成本节约性。
该技术可用于密封袋式电池片,防止铝箔起皱,从而延长电池的使用寿命。也可用于烘干电池铝箔、对太阳能电池板进行光浸润、对特定材料(例如钢和硅晶圆)的待加热区域进行精准处理等等应用中。激光抛光技术的机理是表面窄熔和表面过熔,依靠的是表面的重熔和激光重熔层的再凝固。当金属表面被足够高能量的激光所照射时,其表面经受一定程度的重熔,再分布和通过表面拉应力和重力的作用下,在凝固之前实现了光滑表面。熔化层的整个厚度小于波谷到波峰的高度,从而让整个熔化的金属填充到附近的波谷中,这一填充的驱动力是通过毛细效应来实现的,而较厚的熔化层则会促使液体金属从熔池中心向外流动,驱动力是热毛细效应或马可尼效应,从而让其重新分布。
应用案例如轻型大型望远镜光学部件(尤其是大尺寸和复杂形状反射镜)的材料碳化硅陶瓷。RB-SiC作为一种典型的高硬度、复相材料,表面精密抛光技术困难,效率较低。通过飞秒激光对预涂有Si粉的RB-SiC表面进行改性,仅经过4.5小时的抛光,即可得到表面粗糙度Sq 为4.45 nm的光学表面,与直接研磨抛光相比,抛光效率提高了3倍以上。激光抛光还广泛应用在模具、凸轮及涡轮叶片的抛光方面。
激光冲击强化也称做激光喷丸,是将高能量密度、高聚焦、短脉冲激光(λ=1053nm)辐照金属零件表面,表层金属(或吸收层)在高功率密度激光的作用下瞬间形成等离子体爆炸,爆炸冲击波在约束层的束缚下向金属零件内部传递,使表层晶粒产生压缩塑性变形,在零件表层较厚范围内获得残余压应力、晶粒细化等表面强化效果。对比传统的机械抛丸具有以下优势1.定向性强:激光以可控的角度作用于金属表面,能量转换效率高,而机械弹丸撞击角度随机;
2.作用力大:激光喷丸等离子体爆破产生的瞬间压强高达数GPa;功率密度大:激光冲击峰值功率密度达到几到几十GW/cm2;3.表面完整性好:激光冲击对表面几乎无溅射效应,而机械喷丸后,表面形貌受损产生应力集中。激光冲击后的最大压应力值更优,表面残余压应力提高约40%~50%,对工件的耐疲劳寿命、抗高温和弯曲成型等相关指标数值上都有显著提升。目前已应用在飞机表面处理、航空发动机表面处理等领域。
深圳水滴激光作为国内激光清洗领域头部企业,在激光表面处理技术的其他方向也进行了卓有成效的开发与应用。