前言
激光焊接与传统焊接相比具有热输入量及热影响小、深宽比大、焊接过程自动化等优点。铝合金质量轻、韧性好,屈强比高、加工成形容易,广泛用于容器、机械、电力、化工、航空、航天等焊接结构的产品上,采用铝合金代替钢板材料焊接,可大大减小结构质量。铝是较为活泼的金属,电离能低、导热性很高,表面极易形成难熔的Al2O3膜,在焊缝中容易形成未熔合、气孔、夹杂、热裂纹等缺陷,降低焊接接头的力学性能。与钨极氩弧焊或熔化极氩弧焊相比,激光焊接焊缝窄、热影响区小,搭接接缝减少,焊接过程精密可控,可以实现自动化。目前,激光焊接主要用于薄壁电子元器件、结构件、航天件等,研究万瓦级的光纤激光器用于大厚板深熔焊接是未来发展趋势。
1 铝合金分类和焊接性
铝及铝合金可分为1000系(工业纯铝)、2000系(Al-Cu 系)、3000系(Al-Mn 系)、4000系(Al-Si)、5000系(Al-Mg)、6000系(Al-Mg-Si)和7000系(Al-Zn-Mg-Cu)。按工艺特点铝合金又可分为变形铝合金和铸造铝合金,其中变形铝合金分为两类:非热处理强化铝合金和热处理强化铝合金。
不同铝合金焊接性能各异,比如非热处理强化的铝及铝合金1000系列、3000系列和5000系列具有良好的焊接性4000系合金的裂纹敏感性极低,对于5000系合金,当ω(Mg)=2%时合金产生裂纹,随着镁含量升高,焊接性能有所改善,但延展性、耐蚀性变差。2000系、6000系和7000系合金的热裂倾向较大,焊缝成形不良,焊后时效硬度显著降低。
综上所述,对于铝合金焊接需采用合适的工艺措施,正确选择焊接方法和填充材料,以获得性能良好的焊接接头。焊接前可对材料进行表面处理,使用有机溶剂去除油污 灰尘,随后再在 NaOH 溶液中浸洗,用流动水将表面碱液冲洗干净后再进行光化处理,处理过的焊件在 24 h 内进行焊接工艺实验。
2 铝合金激光焊接中存在的主要问题
激光焊接是以激光作为高能密度光源,具有加热快和瞬时凝固的特点,深宽比高达到12:1但是由于铝合金具有高的反射率和良好的导热性以及等离子体的屏蔽作用,焊接时不可避免地出现一些缺陷问题,其中最主要的两个缺陷是气孔和热裂纹。由于铝合金对激光的反射很强,铝合金激光焊接首先遇到的问题就是如何有效地提高材料对激光的吸收。基于铝合金自身的一些特点,也使得激光焊接工艺更加复杂,亟待改进和完善。
2.1 激光吸收率
材料对激光的吸收率越高,或传热系数、导温系数越小,激光能量越易被材料表面吸收,表面温度迅速上升,材料熔化或蒸发。
各种金属对不同波长激光的反射率如表 1 所示,各种金属的反射率随波长变短而降低,并且Ag、Al、Cu 对激光的反射率高达90%以上,这无疑增加了激光加工的困难 在室温下,铝合金对 CO2 激光的吸收率极低,98%的激光能量将被铝合金表面反射,Nd:YAG 激光的反射率也达80%。可见,铝合金具有对激光的反射率高、吸收率小的特性。这是因为铝合金中自由电子的密度很大,在光波电磁波强烈震动下产生强烈的反射波和较弱的透射波,反射波不易被铝合金表面吸收,因而常温下铝合金表面对激光具有较高的反射率。
2.2 “小孔”的诱导和稳定
在激光焊接过程中,当激光能量密度大于 3.5*10^6W/cm2时会产生离子体,焊接方式以深熔焊方式进行,其原理主要是“小孔”效应,“小孔”的出现可大大提高材料对激光的吸收率,焊件在高能密度下熔合,以获得良好的焊接效果 在铝合金的激光焊接中首要的问题是小孔的诱导和维持稳定的困难,这是由于铝合金本身材料特性和激光束的光学特性造成的。如前所述,常温下的Al能反射掉80%的能量,再加上其导热性好,要产生“小孔”就需要一个大的激光能量密度阈值。不同铝合金激光焊接加工中都存在这样一个阈值,一旦输入功率大于此值,激光能量向材料内部的传递不再受热传导的限制,焊接则以深熔焊方式进行,激光辐射将引起母材金属强烈蒸发并形成蒸发凹槽,激光束通过蒸发凹槽深入到材料内部,焊缝深度和焊接效率也急剧增大。对于高反射的材料来说,如铝合金、铜合金,焊接中需要提供非常大的功率密度,这样就对焊接机型以及准直聚焦镜的选择都有一定要求。
2.3 焊缝的机械性能
细晶强化、固溶强化、时效沉淀强化是铝合金的几种强化机制,即使存在这些强化机制,激光焊接过程中 Mg、Zn 等低熔点合金元素的大量蒸发,也会导致焊缝下沉,硬度和强度下降。瞬时凝固过程中,细晶强化组织转变成铸态组织后,其硬度、强度会有所下降。此外,焊缝中裂纹、气孔的存在导致抗拉强度降低。总之,接头软化问题是铝合金激光焊接中存在的又一难题。
2.4 气孔
铝合金的激光焊接过程中容易产生气孔,主要有两类:氢气孔和匙孔破灭产生的气孔。
(1)氢气孔。铝合金在高温下表面极易形成氧化膜,氧化膜容易吸附环境中的水分。激光加热时,水分分解产生氢,而氢在液态铝中的溶解度约为其在固态铝中溶解度的20倍。在合金瞬时凝固过程中,由液态铝向固态转变时,氢的溶解度急剧降低,液态铝中多余的氢如果不能顺利上浮溢出就会形成氢气孔。这类气孔一般形状规则,尺寸大于树枝晶尺寸,在其内表面可见有树枝晶结晶凝固花样。
(2)匙孔塌陷。焊接小孔内在自身重力和大气压力处于平衡态,一旦平衡被打破,熔池中液态金属不能及时流过来填充就会形成不规则孔洞,有研究发现孔洞内壁镁的含量约为焊缝附近的4倍。
由于激光焊接的冷却速度太快,氢气孔问题更加严重,并且在激光焊接中还多了一类由于小孔的塌陷而产生的孔洞。
2.5 热裂纹
铝合金属于典型的共晶型合金,焊接时容易出现热裂纹,包括焊缝结晶裂纹和HAZ液化裂纹。通常结晶裂纹出现在焊缝区,液化裂纹出现在近缝区。铝合金中尤其6000系列Al-Mg-Si合金裂纹敏感性大,母材经历了快速加热和冷却,在瞬时凝固和结晶过程中,由于存在较大的过冷度,晶粒沿垂直焊缝中心方向生长,在柱状晶边界形成Al-Si或Mg-Si、Al-Mg2Si等低熔点共晶化合物,削弱晶面结合力,在热应力作用下易产生结晶裂纹。在铝合金焊接过程中,诸如一些低沸点元素(Mg、Zn、Mn、Si等)容易蒸发、烧损,焊速越慢,烧损越严重,从而改变焊缝金属的化学成分。由于焊缝区成分偏析会发生共晶偏析而出现晶界熔化,在应力作用下会在晶界处形成液化裂纹,降低焊接接头的性能。
3 铝合金激光焊接工艺
为了实现激光对铝合金的焊接,解决上述存在的问题,目前主要从以下几个方面加以解决。
3.1 气体保护装置
铝合金中低熔点元素损失影响最大的因素是气体从喷嘴喷出时的压力,通过减小喷嘴直径,增加气体压力和流速均可降低Mg、Zn等在焊接过程中的烧损,同时也可以增加熔深。吹气方式有直吹和侧吹两种,还可以在焊件上下同时吹气,焊接中根据实际情况选择吹气方式。
3.2 表面处理
铝合金对激光具有高反作用,对铝合金进行适当的表面预处理,如阳极氧化、电解抛光、喷沙处理、喷砂等方式,可以显著提高表面对光束能量的吸收。研究表明, 铝合金去除氧化膜后的结晶裂纹倾向比原始态铝合金大。为了既不破坏铝合金表面状态,又能简化激光焊接工程工艺过程,可以采用焊前预处理的办法升高工件表面温度,以提高材料对激光的吸收率。
3.3 激光器参数
焊接激光器分为脉冲激光器和连续激光器,脉冲激光器波长1064nm时光束特别集中,脉冲单点能量比连续激光器的大。但是脉冲激光器的能量一般不超过 ,所以一般适用薄壁焊件。
3.3.1 脉冲模式焊接
激光焊接时应选择合适的焊接波形,常用脉冲波形有方波、尖峰波、双峰波等,通常一个脉冲波时间以毫秒为单位,在一个激光脉冲作用期间内,金属反射率的变化很大。铝合金表面对光的反射率太高,当高强度激光束射至材料表面,金属表面将会有60%-98%的激光能量因反射而损失掉,且反射率随表面温度变化。因此一般焊接铝合金时最优选择尖形波(见图1 )和双峰波,波形上升阶段是为提供较大的能量使铝合金熔化,一旦工件中“小孔”形成,开始进行深熔焊时,金属熔化后液态金属对激光的吸收率迅速增大,此时应迅速减小激光能量,以小功率进行焊接,以免造成飞溅。此种焊接波形后面缓降部分脉宽较长,能够有效地减少气孔和裂纹的产生。采用此波形,使焊缝熔化凝固重复进行,以降低熔池的凝固速度。此波形在焊接种类不同样品时可做适当调整。
选择合适的离焦量也可减少气孔的产生,离焦量的变化对焊缝的表面成形和熔深均有很大的影响,采用负离焦可以增加熔深,而脉冲焊接时,正离焦会使焊缝表面更加平滑美观。
由于铝合金对激光的反射率较高,为了防止激光束垂直入射造成垂直反射而损害激光聚焦镜,焊接过程中通常将焊接头偏转一定角度。焊点直径和有效结合面的直径随激光倾斜角增大而增大,当激光倾斜角度为40°时,获得最大的焊点及有效结合面。焊点熔深和有效熔深随激光倾斜角减小,当大于60°时,其有效焊接熔深降为零。所以倾斜焊接头到一定角度,可以适当增加焊缝熔深和熔宽。
另外,铝合金激光焊接时,焊接速度越快,越容易出现裂纹。因为焊接速度过快,过冷度大,焊缝区晶粒细化,形成了大量同方向生长的“束状晶”,在束状晶之间的晶面上有利于裂纹的产生。而焊接速度过快,焊件熔深相对变小。
3.3.2 连续模式焊接
采用传统的激光焊接时会出现脆化甚至裂纹,使用连续激光器焊接由于其受热过程不像脉冲机器骤冷骤热,焊接时裂纹倾向不是很明显,光纤激光器焊接大部分铝合金不会脆断,焊后有一定的韧性,优势明显。
工业纯铝用脉冲激光焊能很好地焊接,焊后一般不会出现裂纹,但现在有些行业,焊后表面需要打磨,而激光脉冲焊后会有凹陷,打磨量会增加,这增加了加工周期和生产成本,而连续激光器可以很好的解决这些问题。电池壳体的封口以脉冲激光焊和连续激光焊焊后焊缝对比如图2所示。由图2可知,脉冲焊点不均匀,咬边,表面有凹陷,飞溅较多,焊后强度不高。为了改善焊缝质量,采用连续激光器焊接,焊缝表面平滑均匀,无飞溅,无缺陷,焊缝内部未发现裂纹。
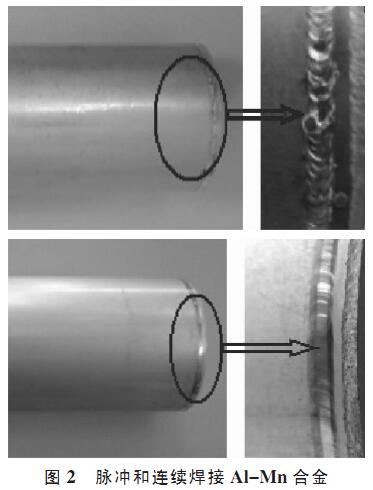
氩弧焊时易出现弧坑,激光焊也一样,收尾时易出现小坑,可在焊接时通过渐进渐出的方式来改善,即在波形中设置一个缓升缓降阶段;另外焊接时可以适当提高焊接速率,以避免出现小坑。
在铝合金的焊接方面,连续激光器的优势很明显 与传统的焊接方法相比,生产效率高,且无需填丝;与脉冲激光焊相比可以解决其在焊后产生的缺陷,如裂纹 气孔 飞溅等,保证铝合金在焊后有良好的机械性能;焊后不会凹陷,焊后抛光打磨量减少,节约了生产成本 但是因为连续激光器的光斑比较小,所以对工件的装配精度要求较高。
3.5 引入合金元素
防止热裂纹的产生是铝合金激光焊接的关键技术之一。6000系列合金有很强的裂纹敏感性,当ω(Mg2Si) =1%时就会出现热裂纹,通过添加合适的合金元素来调整熔池化学成分加以改善,如添加Al-Si 或者Al-Mg-Si粉,对减少裂纹有一定好处。另外还可以通过送丝的办法来改善焊接效果,获得均匀的焊缝,焊缝硬度也有所提高 熔合区枝晶中Mg、Si的含量因填充材料的引入浓度增加,β〃固熔强化作用会增加接头的强度。通常在6063和6082铝合金中填入Al-5Si和Al-7Si焊丝,6013和6056板分别使用CO2和Nd:YAG激光器焊接,填Al-12Si焊丝。
3.6 其他工艺方法
针对铝合金激光焊接过程的稳定性及焊缝质量问题,当前,铝合金激光焊接的研究热点是采用复合工艺,即将激光的高能量密度和电弧较大的加热范围耦合,充分发挥了两种热源自身的优势,兼并了高能密度光束质量和稳定电弧的特性,相得益彰。对于铝合金这类高反材料,采用激光复合焊接可使电弧能量将材料表面预热或熔化,大大提高铝合金对激光能量的吸收 。T.Shida 等人采用 10 kW的 CO2 激光器与 TIG 和 MIG 电弧复合对铝合金进行焊接,引入电弧很大程度上提高了激光能量利用
率,焊缝熔深比也提高了 5% -20%,同时焊缝表面成形平滑良好。激光复合焊通过激光束与电弧的耦合,增加了熔池的几何尺寸并改变了材料在熔化状态下的流态条件,有利于气孔的排除。
双光束焊接铝合金也是一种消除气孔的办法,采用 6 kW 连续光纤激光器进行了 5052 铝合金双光束对接焊,研究了双光束并行与串行排列两种模式焊接时以及不同焊接速度下的焊缝形貌和组织研究发现,采用双光束以并行方式焊接的焊缝中存在较大孔洞,以串行方式焊接铝合金可获得良好的焊缝成形,不会出现气孔。
(作者:大族激光,李小婷 朱宝华 )